The company
VitaLys produces the amino acid lysine which is added to pig feed. The addition benefits the environment, because lysine reduces the need to give the animals soy protein. And thanks to a research project, lysine can now be produced more efficiently.
By Morten Andersen
"We are up against competitors much larger than us, and are exposed to fierce competition. We have to offer highly competitive prices to survive and to develop our business. "
Kjeld Kjeldsen, Cheif Operating Officer at VitaLys
Pig producers reap both environmental benefits and economic benefits when they add lysine to animal feed. Therefore, that a research project has enabled more efficient lysine production benefits both industry and the environment. It will encourage more producers to use the product.
Common sense
Lysine is an essential amino acid which pigs need in high volumes during their growth. Traditionally, pigs were fed lysine by adding soy protein to their feed. However, there are limits as to how much soy a pig can eat without experiencing stomach pains. And soy not only contains lysine, but also a number of other substances which pigs also have in sufficient quantities. This results in waste and increased emissions of nitrogen from pig production.
VitaLys Denmark's only lysine producer, collaborates with DTU Biosustain (Novo Nordisk Foundation Center for Biosustainability). The company produces the amino acid in fermentation tanks where Corynebacterium glutamicum converts sugar into lysine. DTU researchers are now helping the bacteria perform even better.
The bacteria factory
Even though Corynebacterium glutamicum is well-suited for converting glucose into lysine, the bacteria are not, however, naturally optimized for that purpose.
Most microorganisms have some metabolic steps which were previously necessary, but are a waste of energy today. And, of course, the bacteria do not know that they serve as a lysine factory, so they also produce small amounts of other substances.
By activating or deactivating enzymes, we can influence the bacteria to eliminate some of the steps in their cycle, which are a waste of energy from our point of view. Similarly, we can reduce the quantities of the other substances which are manufactured, so that most of the sugar ends up becoming lysine," says Professor Jochen Förster, DTU Biosustain.
The project aim is to increase efficiency by 15 per cent. In other words, to get 15 per cent more lysine out of every kg of sugar you pour into the fermentation tank. This both makes the VitaLys product more competitive and eco-friendly because the production is streamlined without increasing the consumption of energy and raw materials.
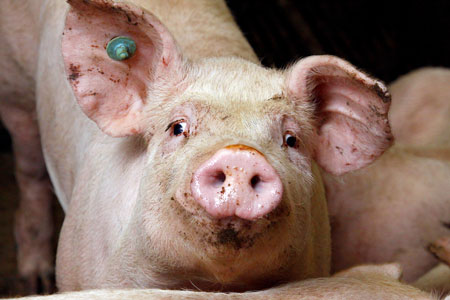
Digging deeper
VitaLys is already at a high-tech stage. Production runs 24/7, and the factory is automated to the extent that it only takes two employees to keep it running at night and on weekends. And the company adheres to a routine of continuously refining its bacterial strain to prevent it from losing its value. The principle is called classical strain improvement protocol.
“Even though we have come a long way, we could see that we had to perform even better to withstand the competitive pressure from producers around the world. We simply had to ‘dig deeper’ than we were capable of ourselves,” says Kjeld Kjeldsen, Chief Operating Officer at VitaLys.
The solution was to contact DTU Biosustain where a research project was created. The driving force in the project is an industrial postdoc, Stefan Wieschalka, who divides his time between VitaLys and the research centre in Hørsholm. He is supervised by both Kjeld Kjeldsen and Professor Jochen Förster from DTU Biosustain.
Benefits everyone
Not only VitaLys, but also DTU Biosustain will benefit greatly from the collaboration, emphasizes Jochen Förster:
"We want to brand ourselves as being capable of improving the bio-processes already in operation at companies. In this way, the project matched our profile perfectly."
Article from DYNAMO no. 39, DTU's quarterly magazine in Danish.

The company VitaLys was founded in 2004, and currently has 48 employees. The company was established as the result of a strategic decision made by VitaLys’s parent company DLG, which, among other things, produces feed to the agricultural sector.
Due to the major Danish pig production, DLG's customers have a great need for lysine. And historically, world market lysine prices have seen significant fluctuations. Therefore, DLG wanted to obtain a better security of supply by setting up a Danish production.
VitaLys produces around 20,000 tonnes of lysine annually, corresponding to one per cent of the world market.
“We are up against competitors much larger than us, and are exposed to fierce competition. We have to offer highly competitive prices to survive and to develop our business,” says Kjeld Kjeldsen, Chief Operating Officer.