LEGO cars helps students understand the complexity of modular production and product development, helping them to prepare for the real world that awaits after graduation.
By Mie Borggreen Winther
The ‘Technology Platforms and Architectures’ course at DTU Mechanical Engineering is heavy on theory, and the course foundations are modular product development, production, and process optimization.
When it comes to putting theory into practice—in addition to a product—what is required are customers, suppliers, and an up-and-running factory. When something goes wrong, it can prove a costly affair. But how do you give students an insight into the real world for which they are training?
You get them to play with Lego bricks.
PhD student Martin Løkkegaard who is affiliated with the course as a teaching assistant, drew inspiration from a summer course at the Massachusetts Institute of Technology (MIT) in 2016, where a simulation game with LEGO cars encapsulated the factory production cycle. The first trial run of a DTU version of ‘The Modularization Challenge’—as he calls it—took place on the last Thursday in March.
At 8 a.m., the students assemble in Building 421. The course counts 80 students, and in groups of eight to ten people, the participants are asked to form teams with a special distribution of roles: A supplier, a customer, a factory manager—with the rest of the team assuming the role of factory workers.
In three, 30-minute rounds, the students are assigned production tasks which must be solved with a view to generating a profit. By selling their product to the customer, they earn money to buy more parts from the supplier, thus boosting production and sales.
Professor Niels Henrik Mortensen sees the game as an opportunity to give the students a sense of production in the real world—in an engaging way.
"Turning it into a game is a more interesting and engaging approach to learning."
Professor Niels Henrik Mortensen, DTU Mechanical Engineering
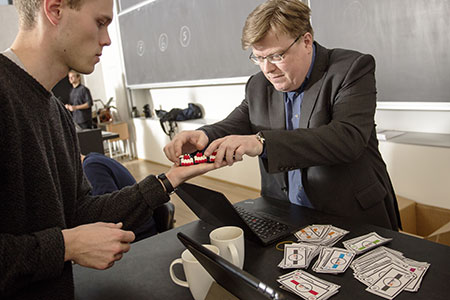
Not total chaos
No fewer than 70,000 bricks—carefully divided into shapes, colours, and purpose—are needed in order for the students to carry on production throughout the game. During the first round, Martin Løkkegaard monitors the students. However, it is not only the students who have to roll up their sleeves—in the role of the customer, Professor Niels Henrik Mortensen must sit at his laptop computer and update all deliveries from his team.
In the first round, production is high. Martin Løkkegaard had expected as much, as the students only have to produce one type of car. All the cars’ chassis are given a serial number by the supplier. The number is then entered on a Google spreadsheet with the time of sale to the factory. Here, it is used for developed currency—modularization money—for when the factory buys chassis modules.
It falls to the factory managers, however, to record the production start and end times of the individual serial number—and as soon as the vehicles are completed, they are quickly sent ‘downstairs’ to a customer waiting to purchase the finished products—assuming they are properly assembled.
One of the pitfalls in the game is that the students lose money each time the customer finds a fault in the product. On the other hand, they can also generate revenue by delivering a certain number of cars at a time and in this way strategically increase their profit by organizing production following a given rhythm.
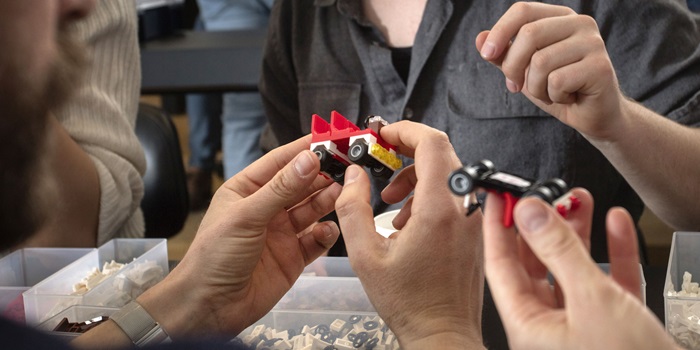
Complex to follow
Round two is much harder, as the students have to produce three different types of LEGO cars, each with its own chassis. Now the students have their hands full, as the supplier has to number three different types of module and keep up with demand from the factory, which can double its revenue by selling the cars in sets of three—one of each kind.
The factory runner—who is in contact with both supplier and customer—must therefore race back and forth in order to keep things running smoothly. Anders Rafn is seated on the back row in the role of team 1’s supplier.
“We managed to maintain an overview in round one, as there was only one chassis to keep track of. But now, things are becoming more complicated. There’s a lot of stress, and it’s difficult to keep pace, especially with the serial numbers, as you need a system to maintain an overview. That came as a surprise,” he says.
On the other hand he feels that cooperation with the factory team is excellent—and that they are ready at this point to expand the business. “The next step must be to recruit another supplier to the team,” he says confidently.

As expected
In the third and final round, the teams are still required to produce three different types of cars, but this time using the same chassis and several common features in the three models—what the course calls ‘design based on a common platform’.
“Production was much easier in the final round—among other things because everyone now knows their place in the team,” says Peter Bjerrum, team 1's factory manager.
“We produced a lot of cars in round one, but discovered we had the module the wrong way round and ended up losing a lot of time and money. That’s when we realized the importance of quality assurance. In round two, production slowed on account of the different models, and we made a lot of mistakes that held us back. That’s when we really learned how important it is to name and assigning serial numbers,” he adds.
The lessons learned by team 1 were precisely those Martin Løkkegaard and Niels Henrik Mortensen had hoped the students would take from the exercise.
The data collected from the teams’ productions show that the error rate in round one was 1.7 per cent, whereas it rose to 2.7 per cent in round two. However, it fell to 1.7 per cent again in the third and final round, indicating that their theory on modular design also makes sense in practice,” explains Martin Løkkegaard:
“When you look at the number of vehicles produced and the number of errors per round, the overall conclusion is that modular car design—where the vehicles share many common design features while retaining different characteristics—makes good sense.”
In the course of the three rounds, a total of 1,442 vehicles were built—and all the bricks had to eventually be disassembled, sorted, and divided into shapes, colours and purpose, so the game can be reused.
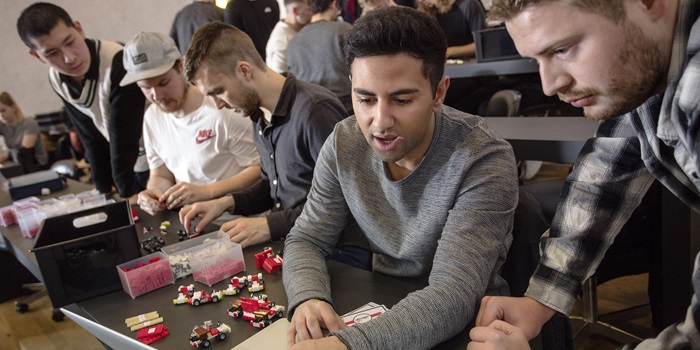