Research
Is there a smarter way to utilize biowaste?
Martin Nielsen asked himself that question three years ago. The answer is yes, but there is still a long way to go before his team’s method for a smarter use of biowaste is ready for industrial application.
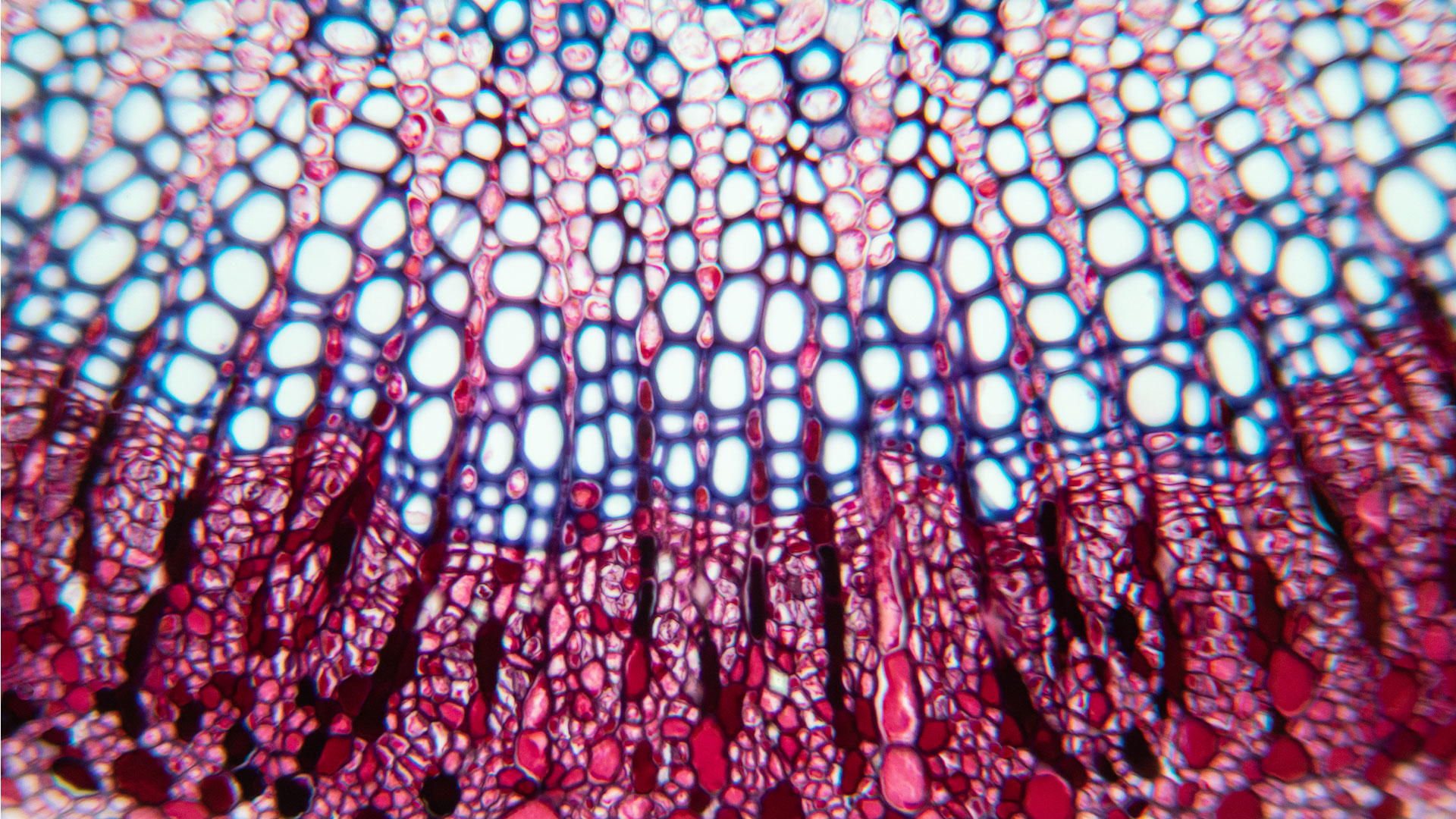
Oops, this feature requires cookies
To view the content, you must change your cookie consent to allow functionality cookies
The stew was a success. All the types of biowaste studied could be converted into varying amounts of GVL. The experiment started with biowaste from nine different types of biowaste, including straw, grass, and beechwood sawdust. The GVL yield varied between 10 and 26 per cent (weight), which was a highly satisfactory result. The greatest yield was achieved with beech sawdust, where the 26 per cent corresponds to almost half of the cellulose and hemicellulose being converted. The lignin in the sawdust was not converted to GVL.
Similar positive results were then obtained with starchy biomass such as rice and potato flour (16-20 per cent yield), and finally, tests were carried out on chitinous biowaste in the form of shells from shrimp and other crustaceans. The chitin structure is similar to cellulose but harder to break down. In this process, GVL was also produced—although in slightly more limited quantities (13 per cent).
A big but
Now that the method has proven effective, you would think that the way was paved for scaling up and commercializing the process. If not for a big but, that is. Because when the stew is ready, GVL can indeed be isolated and used, but the catalyst is still dissolved in the remaining liquid and cannot be extracted and reused. And since the catalyst is extremely expensive, the price of producing GVL with the new method is 1,000 times the amount that would be commercially viable.
There is therefore a need of a solution that brings the costs down, and Martin Nielsen has a good idea of what that solution is. However, this is, so far, a well-guarded secret, and for patent reasons the associate professor cannot elaborate on what the next step should be.
However, Martin Nielsen can reveal that the chosen method has been successfully used for other chemical processes. You would think this to be an advantage in terms of moving forward with the project. But that is not the case—quite the opposite.
For this very reason, the next step is not basic research, and funding from foundations that traditionally support basic research will therefore not be relevant. The DTU researchers have also yet to demonstrate that the process they plan to industrialize actually works, which makes it difficult to obtain funding from foundations that support upscaling and commercialization of research methodologies. Finally, there is not currently an established market for GVL, meaning there is no guarantee the product resulting from the process can be sold. In other words, the researchers are currently stuck in a no-man’s land.
But even though it is a frustrating situation, Martin Nielsen remains optimistic. DTU’s Office for Research, Advice and Innovation, Law & Tech Transfer, and DTU Skylab are specialists in commercializing DTU inventions and assessing opportunities for funding. So, before embarking on any further development of the GVL process, he will join forces with colleagues from these areas.
Read more about the work to transform biomass to GVL in an article in EES Catalysis: Direct biomass valorisation to γ-valerolactone by Ru-PNP catalysed hydrogenation in acid.
Contact
Martin Nielsen Associate Professor Mobile: +45 24651045 marnie@kemi.dtu.dk